Presented by RIVET, Trimble, Ernest D. Menold and Interstate Electrical
Together with Trimble, we recently cohosted the first-ever Construction Productivity Workshop in Philadelphia. We were joined by two contractor partners who walked through the value of having the RIVET Workforce Management platform connected to their Trimble Spectrum ERP. This connection improves Labor Planning and project productivity at their companies.
“Why are we here?” asked RIVET CMO Alison Accavitti. “Labor is the greatest risk. There’s lots of work in construction, and we’re short on labor.”
As our presentation started, she polled the contractors gathered about how they manage their labor.
A quick Labor Planning poll
Labor Planning, more specifically, the act of labor planning every construction project, was under-prioritized for many in the room. The more questions we asked – Who considers labor a challenge in terms of Productivity and profitability? Who’s using whiteboards and spreadsheets for managing labor? – the more hands went up.
When we asked who could measure their project labor estimates to their actual hours or dollars in real-time, someone said they could do it weekly. While that’s not real-time it’s still impressive.
Right up front: Labor Planning itself isn’t a magic wand you can wave at your business to solve your productivity challenges. You need strong Workforce Management business practices in place too, and software to support them.
It’s when you get your ERP or accounting system working in concert that you start seeing changes. Because when you integrate them with a Workforce Management platform, you see what each labor assignment or transfer will cost you on every project. You see where the labor peak is. You see where schedule compression will occur. You’ll see all of this before it sneaks up on you and tanks the job’s profitability. In real-time.
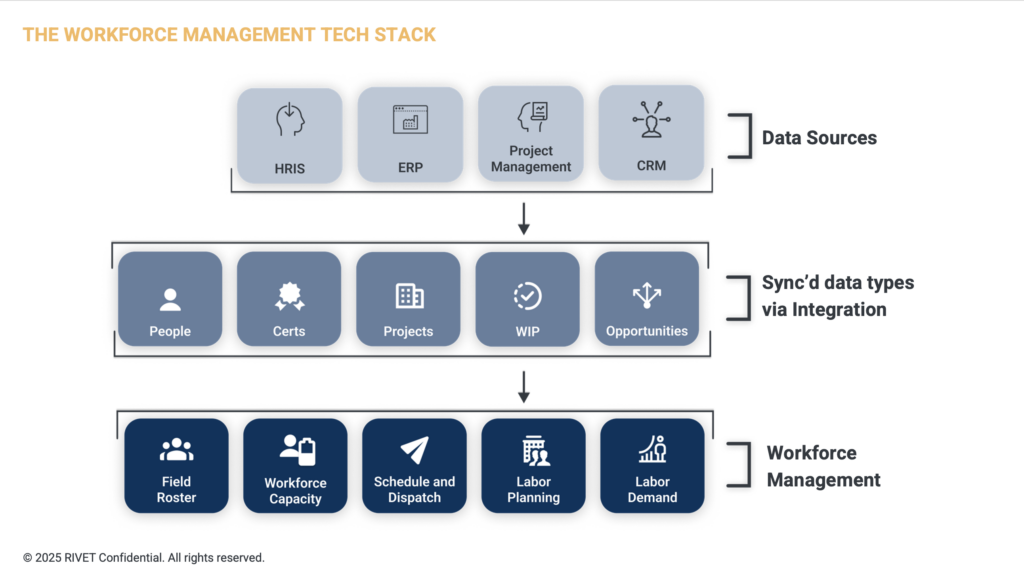
When there’s no end in sight to the worker shortage and labor devours as much as half your budget, can you afford not planning it in advance and then monitoring your burn in real time? And on every job?
“It’s the biggest risk,” Patrick Allen, VP Sales at Trimble said about labor. “It’s the biggest variable to swing that profit margin.”
Ernest D. Menold Inc. talks construction Workforce Management for contractors
Philly-based Ernest D. Menold, Inc. was eponymously founded in 1947. The multi-trade shop has been using the RIVET Workforce Management platform since 2023, and has a Spectrum integration. When there’s a new hire, their personnel info is filed by accounting, and that syncs with RIVET for the new hire’s labor rates and emergency contact info.
Instead of also syncing project data from Spectrum to RIVET, Menold Inc. uses custom projects and assigns labor to them. Vice president Ernest P. Menold’s goal was to free up his superintendent from the “soccer phone tree” when it came to scheduling jobs and dispatching assignments. Phone calls invariably meant small talk, and it’d take 10 minutes just to get a job number. It’s not the worst thing with two-day projects and two-person crews or reactionary work servicing substations and smaller urgent jobs. Bigger crews and longer durations are another story.
“You call this person, who calls that person and then, you know, an apprentice is showing up at 8 AM to a 7 AM start,” he said.
Scheduling larger projects and Dispatching updates with RIVET changed that.
“That was one of our biggest use cases,” he said. “Actually getting that information out.”
Making sure it’s accurate is key, too. The company sometimes accidentally sent labor to the wrong job sites.
“It was just showing up at the right place at the right time with the right information,” Menold said. “I know that sounds so basic, but we hit a point where you’ve got so much information you’re trying to get out over the phone, that so many things get missed.”
Now Menold Inc. pre-fills that information into RIVET and it’s accurately Dispatched when needed.
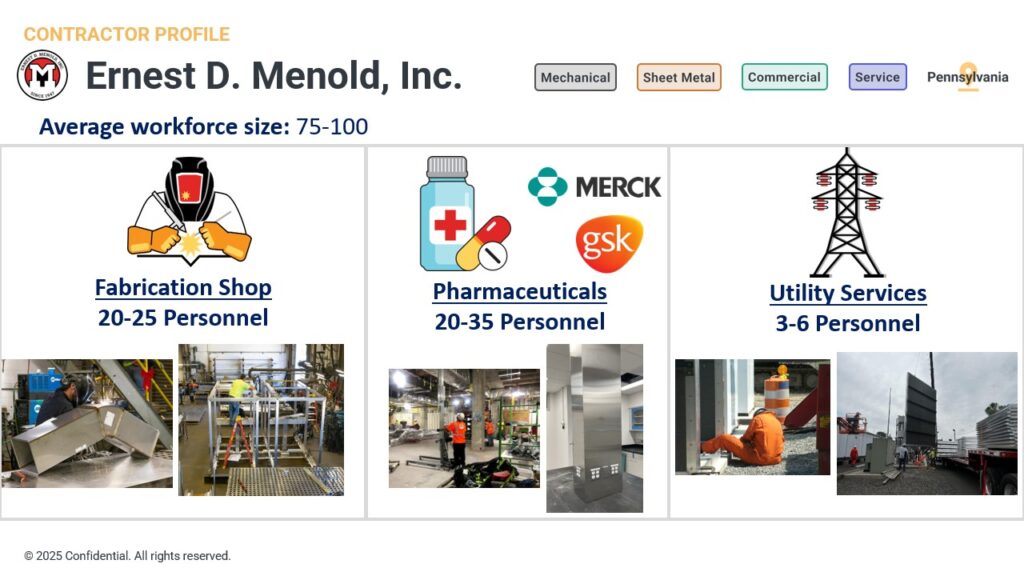
Menold Inc.’s Workforce Management workflows
Burn rate: Because Menold Inc. uses a Spectrum integration, the company doesn’t have to rely on gut instinct to calculate burn rate when a job runs over. “Actually seeing it and seeing a foreman and fourth period apprentice? Oh, I’m at $2,500/day. If it’s a firm price job and we’re two days over, we know we’re around $5,000. Being able to see that representation on the dashboard is very helpful.”
Menold Inc.’s superintendent was paper-based prior to adopting RIVET. Now it takes him “less than a minute” to message an entire crew with the start time, on-site contact (with their phone number), job address and more. This is all set up when the job is created, so everyone always has the same information.
Roster: The Rosters Menold Inc. creates make it easy to dispatch the right labor to the right jobs. And more than that, make sure said labor has the certs to do it. The contractor’s safety manager gets weekly reports of expiring certs, and then proactively gets those workers certified again depending on the types of jobs in pursuit.
Different job sites require different badges, and RIVET allows Menold Inc. to filter its Roster by who has what. Previously, this lived in “10 different spreadsheets.” Menold Inc. does lots of emergency work at airports and who can do it comes down to who has an active TWIC card. Having that information stored in a platform means staffing the job with the right person with the proper badging and certs is simple.
Menold’s worry with adopting RIVET was teaching PMs another login and another password. “I’m always hesitant to push tech on some of them,” the vice president said. “But the whole point is everything’s live in this browser-based solution.”
Team buy-in has been easier because the PMs don’t have to export static information and share it in other formats. When someone says they need two people for three days in Microsoft Teams, a superintendent updates RIVET and then relays that info to the team, streamlining communication further.
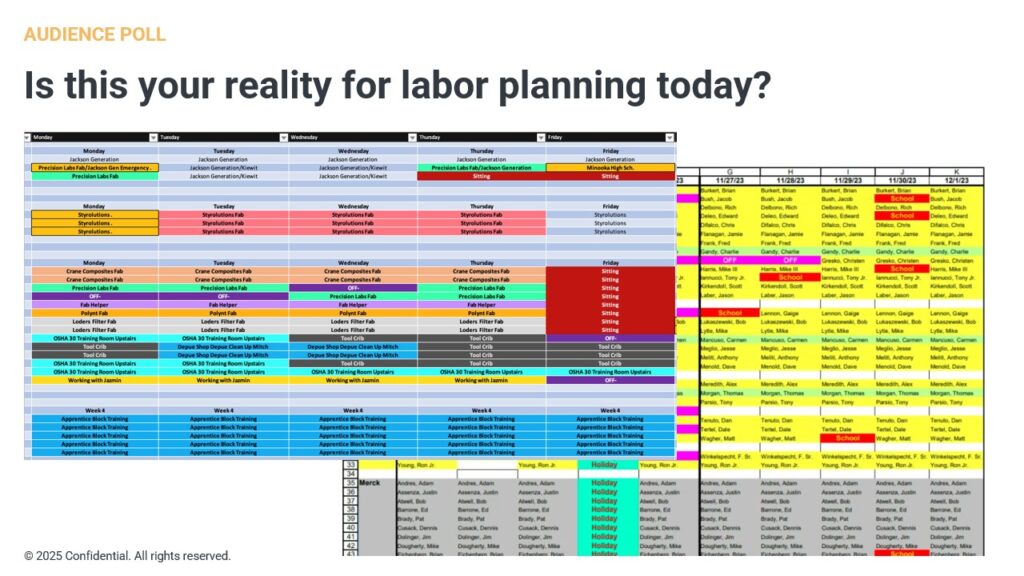
Interstate Electrical Service’s approach to construction Workforce Management
When Steven Drouin was first put in charge of technology at Interstate Electric, he was tasked to automate as much as possible and eliminate redundancies. Previously, the company had multiple systems entering the same information multiple times. The ERP, tool tracking software, estimating software. Each one got the same manually-entered job name and address in each.
“None of them were talking to each other at all,” said Drouin, now senior vice president of technology. The first part of the process was using Trimble Spectrum to standardize project information, so every job has, for example, a ZIP code. This enables him to report on what type of work Interstate’s doing in which parts of the country.
Then came automating time entry, payroll and, ultimately, Labor Planning. Drouin’s journey will be familiar to the lion’s share of contractors: It started with a basic whiteboard. Then he upgraded to a magnetic one. Color-coded spreadsheets came next.
“I swear to God it looked almost identical to Ernie’s [spreadsheet] up there,” he said. “Everybody in this room that’s using a spreadsheet has highlighted and color-coded spreadsheets, and you’re cutting and pasting people from one job to another just so people know where they are.”
Tracking certifications was equally messy because as soon as it was entered, well, the new hire would receive new training and their certs would change as a result. Sure, they were updated in Spectrum, but Interstate’s ERP didn’t connect to anything else in the contractor’s tech stack and giving PMs access to the human resources platform was a no go for obvious reasons.
With the Trimble integration, Interstate measures actuals against estimates and spots trends in real-time. The company can marry pre-construction projects to active projects too. This means Interstate keeps its teams busy across six New England states. Constantly.
“We have 800 employees company-wide and we want to make sure we’re keeping everybody 110 percent active,” Drouin said. He’s proud of the fact that the company has 40 and 50 -year employees. He’s been there for 30.
RIVET helps Interstate maintain the proper amount of work for the labor it has — and avoid hiring more expensive and less productive temp labor.
“We don’t want to send people home and lay them off,” he said. “People are hired for a lifetime.”
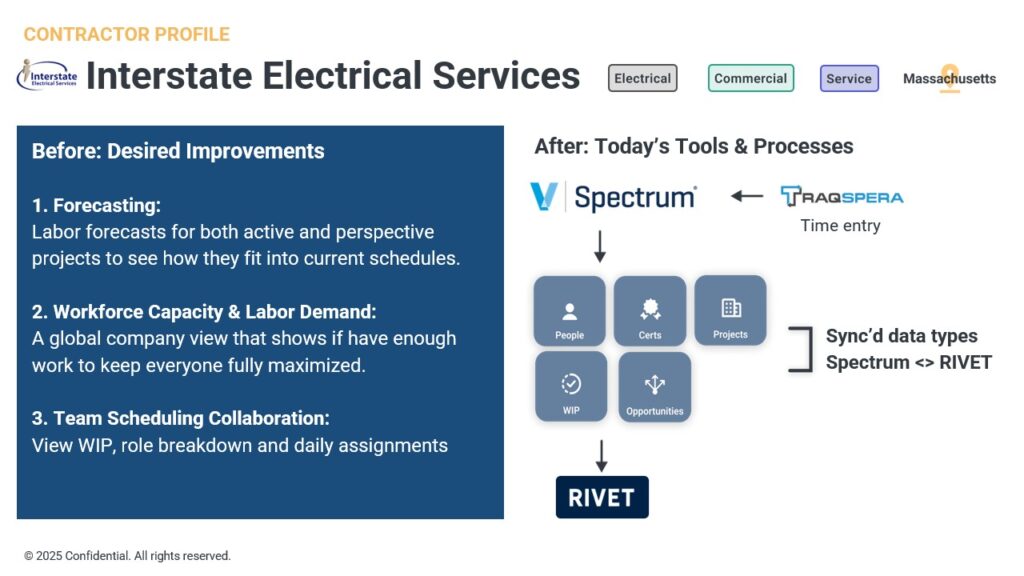
Implementing a Workforce Management platform
Interstate’s RIVET implementation was a slow roll out. The previous WFM platform only got about 15 percent utilization by the PM team, and Drouin wanted to set everyone up for success this time around. He took a phased approach. First bringing on regional managers and their admin teams, training them all and making them experts the first six weeks. Then, he brought in the apprenticeship management team, and had the regional managers and admin teams train PMs through the process. All told, it took roughly two months. Executives were trained as well.
“This is a mandate, everybody has to do this,” Drouin said. “We have to have this global view, especially where we are right now with the economy and the way projects are slowing down and being pushed out because of interest rates and all that happy fun stuff.”
Drouin said that Interstate constantly has to massage the labor pool and move workers to different places when projects get stalled “all the time.”
Menold Inc.’s implementation was different, but similar. For the first three months, a superintendent kept a labor spreadsheet going at the same time as RIVET.
“Really, implementation was just one call with our RIVET account manager and our PM saying spreadsheets no longer needed to be shared,” Menold said. “This is our source of truth.” Now, PMs are starting to request labor via RIVET as the next phase of implementation.
Phasing out phase codes
Interstate started in 1966 and Drouin praised his superintendents as some of the smartest people that work in the company. They know how to make their jobs efficient and the outcomes look good as well.
“So tell me one thing: Tell me if your superintendents have ever had ‘rough’ as a phase code for their job, and they’re going over. That they didn’t put that labor in ‘finish,’” he said. “They do every time and it’s never actually been accurate once.”
Eight years ago, Interstate eliminated phase codes across the company because all the superintendents were doing was spending overheard tracking “something that meant nothing,” Drouin said.
“I find it’s bullshit,” Drouin said. “For real.”
By eliminating phase codes, Interstate made the most expensive person on the job site – the superintendent – 10 times more efficient. What used to take seven hours on a Friday is done in 15 minutes.
Allen from Trimble agreed.
“We hear this a lot,” he said. “It’s a point of diminishing returns. In theory it sounds great having all these buckets and having the guys penciling in how many hours they did. I don’t even know what I did on Monday. And the reports? They suck because they’re all inaccurate.”
Chart your own Workforce Management path
Curious how implementing Workforce Management principles and a software platform built for self-perform contractors can impact your construction business? Download our worksheet and see for yourself.