MEP Project Teams
Are you losing profit in the last 20% of your projects?
A deep dive on the labor peak for MEP contractors


Gary Fuchs is RIVET’s Sr. Workforce Management Advisor. Gary spent 40+ years at Westphal & Company Inc. proving out expert practices for workforce management and labor planning. He later joined LaborChart, acquired by Procore, where he advised contractors across the globe on these practices. We sat down with Gary to do a deep dive on the labor peak.
Start today.
Adopting the RIVET Workforce Management Platform can have a huge impact on your field performance and profitability.
Almost all contractors put together a labor curve during the estimating stage, but few of them understand the depth of what they’ve done.
You’re probably asking yourself, “What the hell does that mean?”
In this scenario, determining a composite wage rate involves creating a list of labor needed in the estimating stage. You know that certain higher paid roles will be there for a longer duration. You start deciding what other roles will report into that hierarchy. When you start doing that, you’re creating a bell curve (a labor resource profile) — whether you know it or not.
“You have a bell curve for every project that you bid, but you’re not aware that you created it,” said Gary. “After the curve is created for the composite rate, it’s abandoned as a tool to use for labor planning. The visual of the curve is missing because it’s embedded in a spreadsheet. You unconsciously abandon the roadmap for the sequence of project labor planning, and you’re about to plow forward with no guideline.”
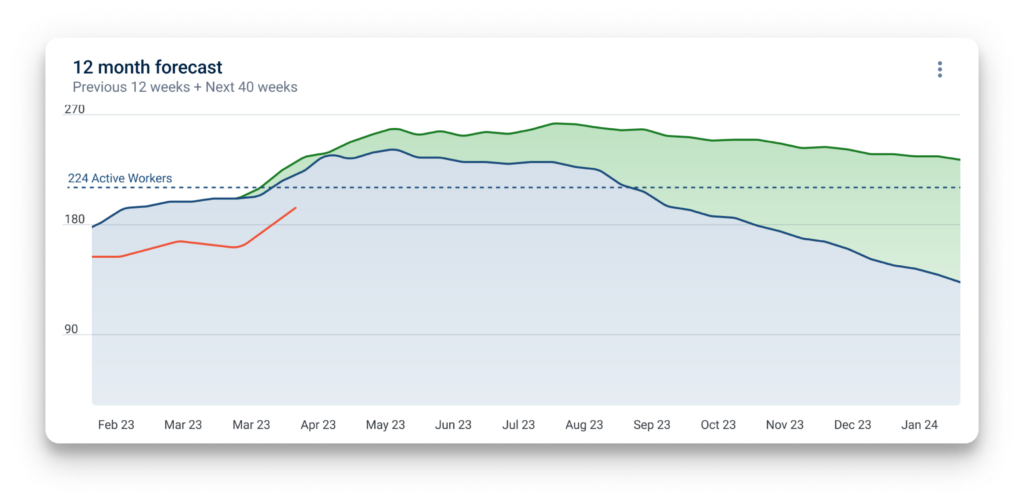
The old-school way of labor management
In Gary’s experience, it’s an industry norm to strive for doing more work with less labor. You need 6 people on the job today, and you’re trying to do it with 4 or 5 over the course of the project. “That’s great, except for when we’re short on people for the job. Imagine a ceiling grid is going up and you don’t have the overhead conduit installed. If we don’t get all of the conduit up before the ceiling goes in, we have to work around the grid with ladders and not man lifts. The idea of saving as much labor as you can early in the project is flawed, but a lot of contractors do that,” Gary said.
“When I was an apprentice, I worked closely with the superintendent at the time. He pounded into my head ‘save labor’ in the early stages, and that’s the industry’s attitude. I operated that way for a long time until I concluded that something was drastically wrong.
Productivity and the labor peak
Fast-forward to a job site in progress. You’ve just reached 80% complete. Gary says this is where the project is vulnerable and the discussions you have will determine success or failure. Are you going to keep your projected profit or experience the dreaded margin fade phenomena?
“This is where you go, ‘oh shit’, we’ve got a problem, and it’s too late,” Gary said. “You’ve created a disaster, and now you’re in the last 20% of the job, and you think you’re a lot farther ahead and the deadline hasn’t moved. Now what? You have no choice. You must add labor. Now you’re walking the plank. You must bring another supervisor and crew, they need to learn the job site, this is a big learning curve. Not only are you pumping people into this job, but they also aren’t 100% productive when show up. Now you’re throwing money at it because you have to get it done. Tools, equipment, labor, safety supervision. Everyone is pulling their hair out? asking what the hell happening. The easy out is blaming it on a bad estimate. This is typically simply not the truth. There is a lack of awareness that the labor was mismanaged or the people responsible for the poor discussions aren’t going to step up. It’s easier to blame the estimate.”

When you get to the peak, you need a punch list:
1. Make a detailed list (punch list) of what still needs to be done.
2. Assign labor hours next to every line item.
Make sure that assessment accurately accounts for logistics to complete tasks, not just the tasks themselves.
3. Determine the total number of labor hours needed.
Compare this to your budget to have a clear understanding of where you are and what you have left. You may find you already have a problem if your ramp up labor plan wasn’t well defined to begin with, and you weren’t monitoring your labor curve.
4. Set goals to get the work done in an orderly fashion.
“Stick to the plan and finish the job. Your foremen will be astonished by this approach. By being proactive, the owner-generated punch list should be minimal. Most loose ends are cleaned up allowing for a clean and orderly closeout.” Gary said.
There is a common opinion that “construction is hard.” And it is hard. Everyone shares in the pain, and that’s the norm.
If your projects are lacking a labor plan, you’re unaware of the peak, you’re lacking a zero punch list and an exit strategy, the impact might look like this:
Project Managers: the job loses a bunch of money, because they don’t have transparency to how labor is managed. “I guess construction is hard with no other explanation.”
Superintendents: they have no idea they screwed up. They’ve been given the responsibility of managing labor but also supervising it — two completely different and equally important responsibilities. Their life expectancy is shorter, they get bags under their eyes, and their hair turns gray. A lot of things they are expected to do should be spread across multiple people (and the project manager is one them).
Good labor planning requires a good tool
Obviously, Gary would recommend MEP contractors use the RIVET Workforce Management Platform for labor planning. But you need to be ready to use it properly.
With RIVET, you are now managing your labor in real time, with controlled transparency for everyone to see, which turns into a very high level of collaboration.
”There is no other way to monitor your labor in real time other than a platform like RIVET,” Gary said. “Contractors ask me, what do you mean real time? Do you mean within a day? Real time is real time, within a second. You get to be so proactive at managing your labor and you start to wonder what you would ever do without it. If you took RIVET away from the contractors that use it, they would struggle and most likely crumble. It’s becomes so engrained in the workflow processes that it’s hard to manage without it., Moreover, if you integrate it with your financials, it’s an indispensable tool.”
Get Started Today
Construction labor challenges can be greatly reduced with the right software